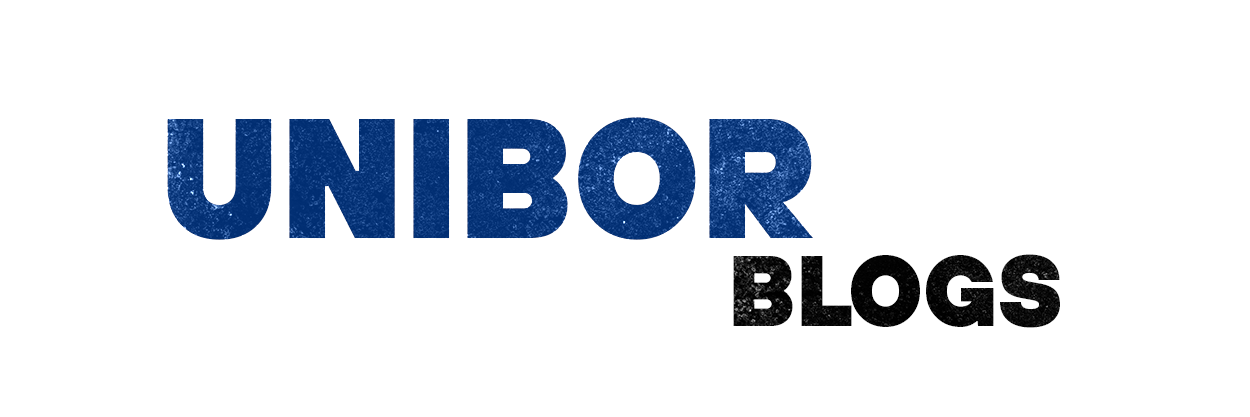
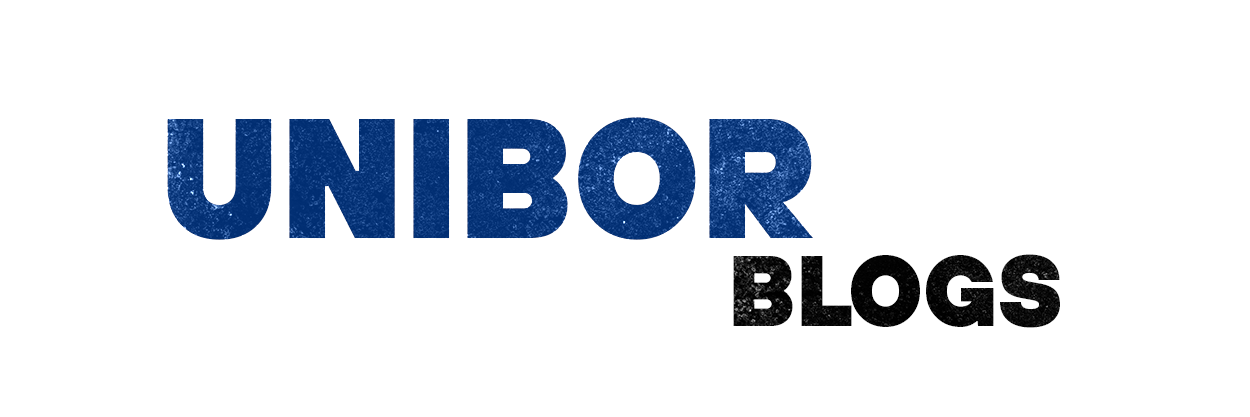
Choosing the right annular cutter is essential to getting the performance you need. Using the right cutter for the job guarantees a solid finish, let’s look at the key factors in choosing the right annular cutter:
How can I choose the right annular cutters?
Annular cutters, often referred to as ‘Rotabroach cutters’, ‘annular drill bits’ and other terms, are a fantastic alternative to traditional twist drills. These tools are generally used with magnetic drills. Choosing the right annular cutter for the job is a crucial part of guaranteeing performance, with different types of cutter designed for different materials.
The diameter of the cutter needs to be big enough to cut the hole correctly, but not too large for accurate use. Alongside this, elements such as cutting depth, material and design are all factors which need to be considered.
Let’s break these factors down into more detail, starting with the annular cutter types available on the market:
HSS Cutters
HSS (High-Speed Steel) cutters are a type of annular cutter made from high-speed steel.
This type of steel is chosen due to its ability to withstand high levels of heat and pressure, making it ideally suited to cutting a wide range of materials. HSS cutters are commonly found in construction and manufacturing industries, chosen due to their cost-effective nature and used to cut holes in a variety of materials.
HSS cutters are generally less expensive than other types of annular cutters, such as TCT (Tungsten Carbide Tipped) cutters, but they are not as durable and cannot cut materials with a higher tensile strength, as well as tougher alloys.
TCT Cutters
TCT (Tungsten Carbide Tipped) cutters are another type of annular cutter which feature tips manufactured from tungsten carbide.
This material is able to withstand high levels of heat and pressure, making it ideal for cutting through tough materials like stainless steel and cast iron. TCT cutters are often used in construction and manufacturing industries, where they are used to cut holes in a variety of materials, including tougher alloys and high tensile steels such as structural steels.
However, this comes at a higher price than the HSS cutter, which is generally considered more cost effective. Though, considering the extended tool life of the TCT cutter, capable of cutting multiple plates back to back without issue, many consider TCT cutters to be a worthwhile investment with solid returns, despite their higher price point than the High Speed Steel option.
What does this tell us?
Just like other tools, annular cutters are available at a range of different prices, each with different levels of performance and specialties.
Therefore, choosing the right annular cutter means choosing the correct price point, if you’re only drilling lower-tensile steels and softer metals, HSS cutters will be suitable. However, if you’re regularly cutting through tougher alloys and other hard metals, TCT cutters may be a valuable addition to the toolbox.
Aside from the material, there’s other crucial elements that go into this decision, such as:
Cutting depth
These cutters come in a range of different cutting depths, often relative to their diameter of cut, which make them suited to different jobs. It’s key to consider the depth of cut required as this is perhaps the most important factor in the drilling process.
The material being cut
Having covered the different types of annular cutter, let’s look at common surfaces and their requirements. Annular cutters are designed to cut through a wide range of metals, including steel, stainless steel, cast iron, aluminium, brass, and copper. Because of this variety, manufacturers produce cutters from different materials, suited to a range of different applications.
For example, HSS (High-Speed Steel) cutters are ideal for cutting through softer metals like aluminium and brass, whilst TCT (Tungsten Carbide Tipped) cutters are suited to cutting through harder metals, including stainless steel and cast iron. It’s essential to choose the right cutter for the job, as using the wrong type of cutter will not only lead to poor performance, but also a drastically reduced tool life and a poor finish on the target project.
Now, let’s take a look at some common questions about annular cutters:
What tool should I use my annular cutters with?
Annular cutters are generally used with a magnetic drill (also known as magnetic drilling machines, core drills or mag drills). These are portable drills which use a magnetic base to adhere to the target surface. Their lightweight construction and powerful motors make them an ideal asset for businesses drilling a number of holes into different metals, across different sites.
Magnetic drills are available from a wide variety of different brands and at different price points, for example Rotabroach offer the Commando 40, a budget-friendly all-rounder, as well as more powerful premium options such as the Element 100 and even impressive low profile alternatives including the Element 50 Low Profile. Used alongside the appropriate annular cutter, these drills are a fantastic asset to businesses and industries across the world.
What is tooth geometry?
Tooth geometry describes the shape, size and arrangement of an annular cutter’s teeth. This part of the cutter determines how smooth and accurate the cut is, with some cutters using specialist geometries designed for efficiency.
Similarly to cutter materials, different surfaces necessitate different geometries. For example, some surfaces need a cutter with sharp, pointed teeth whilst others may require a more rounded tooth geometry. Many manufacturers produce unique geometry, such as Rotabroach and their annular cutter range.
Tooth geometry is therefore a vital part of the annular cutter and it’s performance.
No Related Posts