Metal Cutting Saws
Learn All About Tools.
Want to learn more about metalworking products? Use our search engine to find out more about the range we offer.
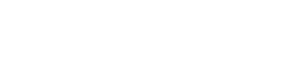
Metal chop saws are amongst the most useful power tools in any workshop, find out more here:
Metal Cutting Saw FAQ’s
-
What is a metal chop saw?
Metal chop saws are an integral part of any larger-scale project, this heavy-duty machine is designed to cut through most materials including dense metals, but can also handle plastic and wood as well as steel, angle iron and other metal stock.
As a high power device, the chop saw makes light work of this wide range of materials through its powerful motor and specialized saw blades, producing accurate cuts quickly. It’s easy to see why metal cutting saws are so valuable in multiple industries and on any scale project, but how do you make sure that you get the right saw for you?
To understand making the right choice in such a varied power tools market, it is important to begin by breaking down some key information about metal cutting saws.
Power Source
Selecting a metal cutting saw with the right power source is crucial to performing work properly, generally speaking there are three different power sources in the majority of saws:
Gas Powered
These saws use a gas powered engine to cut a wide range of metals very effectively. Loud, expensive and heavy, these metal cutting saws offers more power than other options, making it suited to heavy-duty work and large volumes of cutting.
Electric Powered (Corded)
As an alternative to gas powered engines, these models run on electricity from any standard power outlet. They are lightweight and easy to maneuver, however their performance is limited due to the reliance on a power cord.
Electric Powered (Cordless)
These metal cutting saws also run on electricity, however by incorporating a rechargeable battery rather than a power cord. This gives them significantly more flexibility due to their freedom of movement, but they are unable to withstand heavier jobs due to their limited metal cutting power compared with the other two options.
-
What Are The Different Types Of Blades?
There are two primary types of blades used in the metal cutting industry:
Abrasive Disk Blades
These blades are lightweight, affordable and best suited to those starting out with chop saws or working on smaller-scale DIY projects. Whilst more cost-effective, these blades have a tendency to produce sparks and leave cuts with burrs.
The actual cutting process of this type of saw takes place by using a disc similar to that of a grinding wheel, but much thinner. The cutting wheel and motor are mounted on a pivoting arm attached to a fixed base, often utilizing a built-in vice to hold materials steady. The cutting discs are generally about 360mm in diameter and 2.8mm thick, however larger saws can use 410mm diameter discs. Some abrasive saws use discs with diamond and cubic boron nitride which last longer than a conventional blade.
The method of abrasive chop saws essentially involves removing material through grinding, which is fast but produces a lot of noise and mess. Therefore, due to spark production it would be considerably dangerous to use this saw for metal cutting in a flammable environment.
As well as this, whilst the saw is ideal for producing quick cuts due to its high blade speed, an abrasive chop saw will not leave the workpiece with clean edges and its blade can potentially bow during operation, decreasing its accuracy. Because the saw grinds the metal, softer materials such as aluminum risks gumming up the blade and making it useless, meaning this type of saw blade is only appropriate for hard metals including steel pipe. Overall, the abrasive chop saw blade remains amongst popular power tools used in metal fabrication due to its cost-effective nature.
Cold Saw Blades
As a more expensive option, cold saw blades offer a quicker, more accurate cut without producing sparks or heat on the target material. The blades cut metal by utilizing a circular, toothed saw blade and often a liquid coolant, to transfer heat to the metal chips generated during the cut.
This means both the blade and target metal are cool. Cold saws as a machine are generally comprised of a blade and motor connected to an arm, the arm is set to a pivot point to allow the spinning blade to move vertically down through the material during operation.. Larger saws work on the same vertical axis function, but often use autonomous methods to lower the blade instead.
Cold saw blades chip material as the blade spins using the teeth of the saw, unlike their abrasive disk counterpart. They also spin at a considerably slower rpm and are therefore capable of cutting softer meals such as aluminum, as well as harder metals like rebar.
While these are the two main types of metal cutting saw blades, it is not enough to simply choose between the two. A large part of deciding which blade to use is based upon the material being cut.
Cutting Different Materials
Different materials require different things, for example stainless steel and sheet metal will have different requirements, As discussed, an abrasive chop saw blade is more suited to harder metals due to its higher RPM, whilst a cold chop saw blade spins at a considerably lower RPM and therefore is capable of cutting softer metals without gumming up the blade and rendering it useless. It is also worth considering the volume of material stock being cut, for example Rotabroach’s ‘Raptor’ range of saw blades last up to 20 times longer than an abrasive disk, meaning that whilst more expensive, they offers a massive boost in efficiency.
Therefore, if you are using a chop saw for high volume work, or on an industrial scale, it may be worth considering opting for a saw blade with the right level of endurance.
-
What Is The Difference Between a Metal Cutting Saw and a Wood Cutting Saw?
Despite their comparable function, metal cutting saws and wood cutting saws have some key differences. The primary difference between the two saws is their RPM, woodcutting chop saws can be repurposed to cut metal, but the blade speed must be slowed down considerably and replaced with a suitable blade for metal stock cutting. Alongside this, many specific metal cutting saws utilize a form of coolant in order to keep the work piece cool.
-
What Are The Different Types Of Chop Saw?
All of these saws share a swiveling table, alloying different angles of cut into the horizontal plane, as well as revolving blades that travel downwards. However, there are a few key differences that are important to know when deciding on the right tool.
Standard chop saws
The standard chop saw cuts angles in one plane, ‘chopping’ down in one direction. The support table rotates, but the blade cannot move from its upright position. This, of course, limits the blade to cutting stock from the same angle as the arm cannot be moved horizontally.
Compound chop saws
The compound chop saw differentiates itself from the standard chop saw due to its ability to tilt the blade from a vertical position, allowing two different planes for cutting stock. This is an obvious advantage as it allows the machine to perform more tasks without significant adjustment.
Dual compound chop saws
Similar to compound chop saws, these machines can tilt either left or right, allowing more versatile angles and the ability to make bezel cuts without moving the target material.
Sliding-Compound chop saws
This type of chop saw incorporates all the benefits of the aforementioned types, however it also allows the blade to move back and forth, in addition to left and right. This offers more versatility in function and therefore application to a wider range of project.
-
How Can I Use A Chop Saw Safely?
Safe use of a chop saw is consistent with the range of different generic safety guidelines for other power tools, these can be separated into two primary categories:
The Operator
As safe as modern machines have become, there is still an inherent risk of injury to both the operator and those in the immediate vicinity, for this reason responsible use of the equipment is still critical to its safe operation. This includes the physical capacity of the operator themselves, ensuring that the person using the machine is not impaired in any way (through both substances and medical factors) as well as being provided with the requisite training and knowledge to utilize the machine safely.
Wearing appropriate clothing and PPE is also highly significant in minimalizing risk when using a chop saw, inappropriate clothing risks the potential of operator injury due to the high powered nature of this machines and the materials they cut.
The Machine
Most chop saws come with a number of built-in safety features, such as a vice and guard, The blade guard prevents by-product materials from potentially injuring the operator, whilst also protecting the hands during operation.
Therefore, to use a chop saw safely, follow these guidelines:
Check The Cords: If using an electric corded power source, always check the power cord of a chop saw before use to account for any frayed or worn cords, these can present a serious risk to the safe operation of the saw
Wear Appropriate Protection: Usually the first safety measure to be considered, suitable protective gear is of critical importance to ensuring user safety. Gloves, long-sleeve tops and face shields are all highly important to the safe use of a chop saw due to the potential for debris during cutting.
Check The Blade: A damaged saw blade can not only compromise the project itself, but also damage the machine and injure the user. Therefore, it is essential to check blades for dullness, chipping or rust.
Avoid Water: Again, if using an electric saw it is crucial to avoid using the equipment around water due to the potential for shorting or electrocution. Chop saws of this nature should be used and stored in dry areas to reduce risk.
Consider Your Lighting: Working in lower visibility heightens the risk of injury during operation, therefore it is key to consider the environment around you. Consider adding a spotlight or other additional sources if the workplace does not have sufficient lighting.
Maintaining a Chop Saw
Although they are hard-wearing machines, cutting a large amount metal stock will inevitably have an impact on the chop saw’s operation. Therefore, it is important to take a proactive approach to maintaining the equipment, not only to ensure user safety but also to maximize the longevity of the machine. Here’s how:
Keeping The Equipment Clean: Regular clearing of a chop saw is a key part of keeping the machine up and running, removing any debris from both the saw and the workspace around it will ensure a safe, comfortable environment to work in.
Check Components For Damages: Using a chop saw safely and maintaining the longevity of the tool both require the safe attention to detail regarding its components. Wear and tear is a perfectly normal aspect of metal cutting and wider mechanical work, even the most modern, well-maintained machines will experience wear and tear when cutting metal stock and other materials. Therefore, closely inspecting the saw regularly will prolong its lifespan. Key components to look at are the saw blade, checking the teeth and blade for cracks, chips and other wear. As well as this, checking the kerf board and power cord (or motor) are key to proper chop saw maintenance.
Chop Saw Lubrication: Aside from checking the components and cleanliness of the saw, ensuring proper lubrication of the gears. This will keep the saw up and running, preventing, preventing debris from clogging the gears and allowing the user to work on projects quickly and consistently.